CURRENT RESEARCH
smart control for manufacturing system / advanced cnc control
Robot Machining
Human-Factory Interaction
Manufacturing Processes
smart control for manufacturing system / advanced cnc control
CNC (Computer numerical control)는 공작기계를 제어하는 핵심 기술이다. CNC는 공작기계가 신속하고 정밀하게 가공할 수 있도록 경로를 생성하여야 한다. 또한 생성된 가공 경로를 정밀하게 추종하기 위하여 공작기계를 정확하게 제어하여야 한다. 더 나아가 가공 품질, 가공 시간, 에너지 소비량 등을 고속으로 예측하고 최적화하여 정밀도와 생산성을 극대화하는 역할을 수행하여야 한다. 본 연구실에서는 미래 공장에서 요구되는 지능적인 공작기계 제어기 요소 기술 연구와 이를 적용한 시스템 설계와 제작을 수행하고 있다.
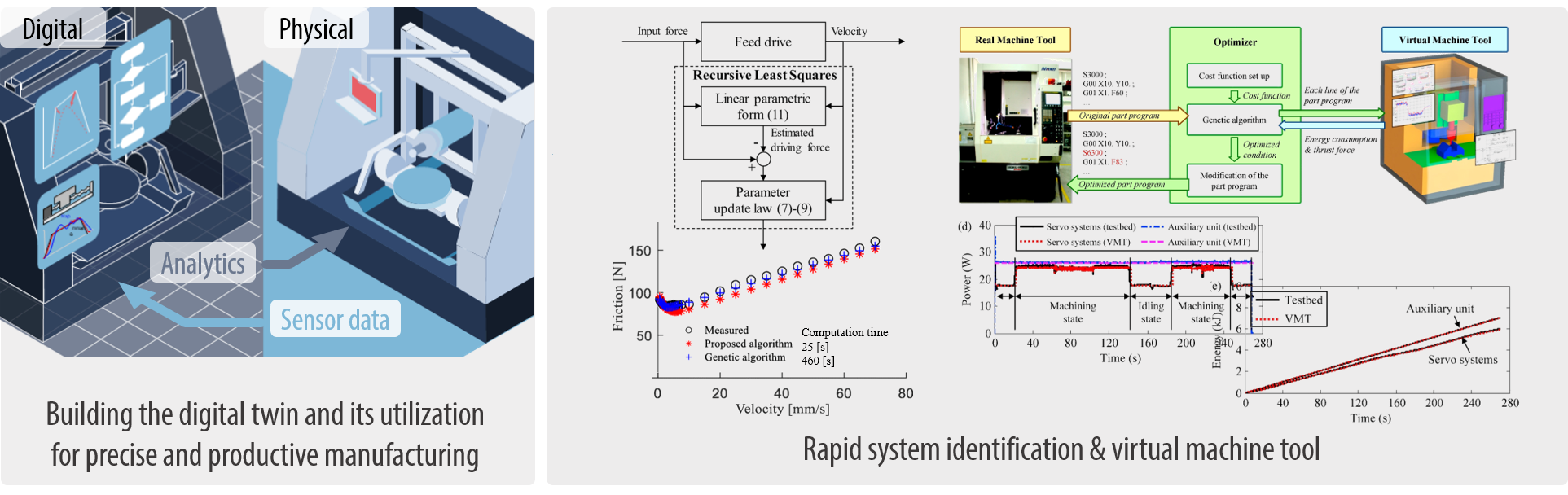
Tool path generation for high-speed & high-accuracy machining
공작기계를 위한 고속 및 고정밀 가공을 위한 경로 생성 알고리즘을 연구하고 있다. 공작기계의 동적, 구조적 특성 등을 고려하여 기계가 정밀하게 추종할 수 있는 경로를 생성하는 연구를 수행한다. 또한 요구되는 가공 공차를 만족시키면서도 고속 가공이 가능한 경로를 생성하는 연구를 수행한다.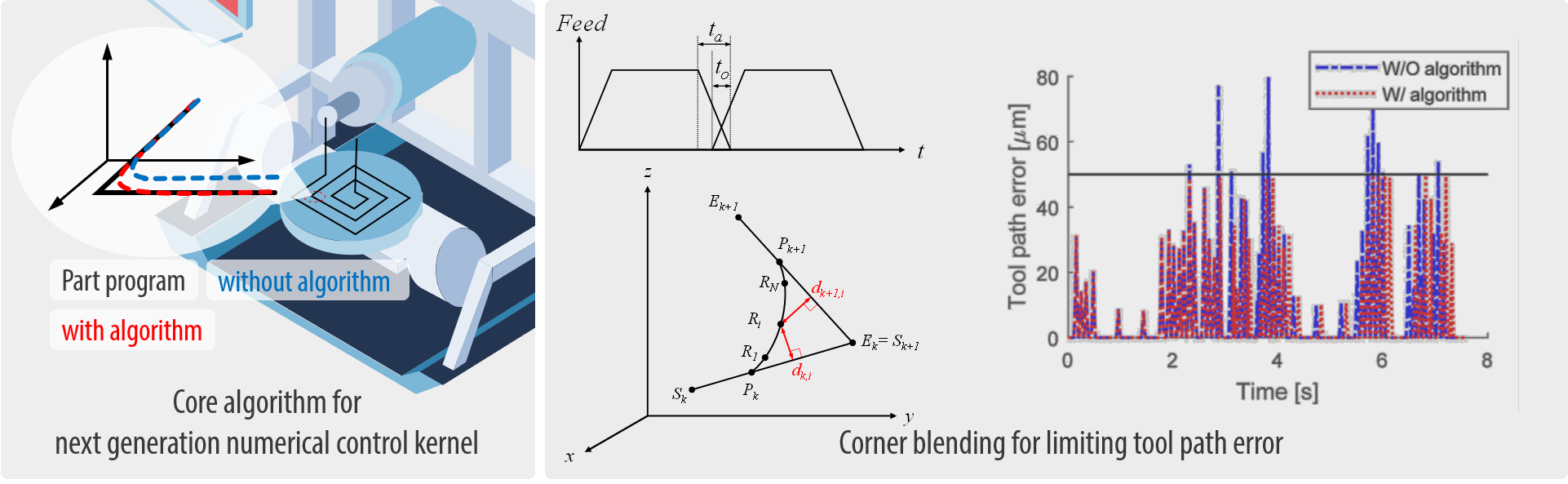
Machine tool precision control
공작기계의 정밀도를 향상시키기 위한 제어 기법을 연구하고 있다. 공작기계 이송계의 동적 특성을 파악하기 위하여 질량, 마찰력 등을 고속으로 식별하는 연구를 수행한다. 또한 식별된 공작기계 모델을 활용하여 위치 오차, 윤곽 오차를 억제하는 제어기를 연구한다.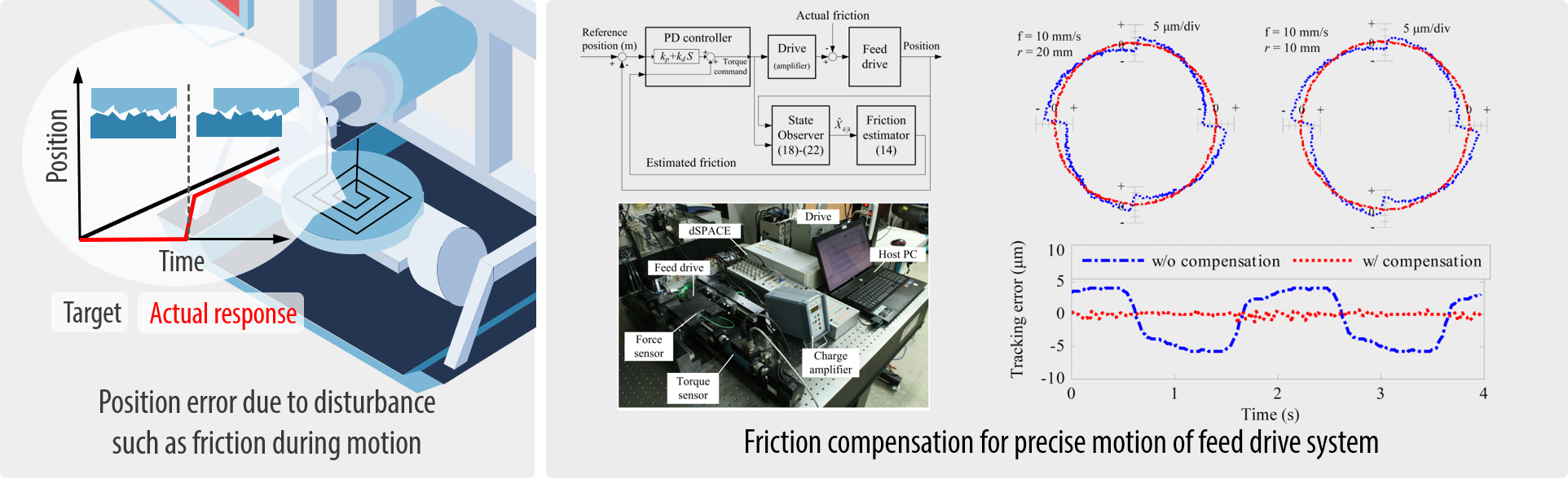
Cyber-physical system for precision machining
공작기계의 정밀도와 생산성을 극대화하기 위하여, 공작기계의 특성을 모사하는 가상의 시스템인 디지털 트윈을 연구하고 있다. 또한 실제 공작기계와 이의 디지털 트윈을 연동한 사이버-물리 시스템을 제작하여 가공 시간 고속 예측, CNC 파라미터 최적화, 충돌 방지, 제어 특성 및 에너지 소비량 고속 예측 및 최적화, 가공 공정 시각화, 잔존 수명 예측 등을 연구한다. 또한 현장에서의 디지털 트윈의 용이한 제작을 위한 시스템 자동 모델링 기술을 연구하고 있다.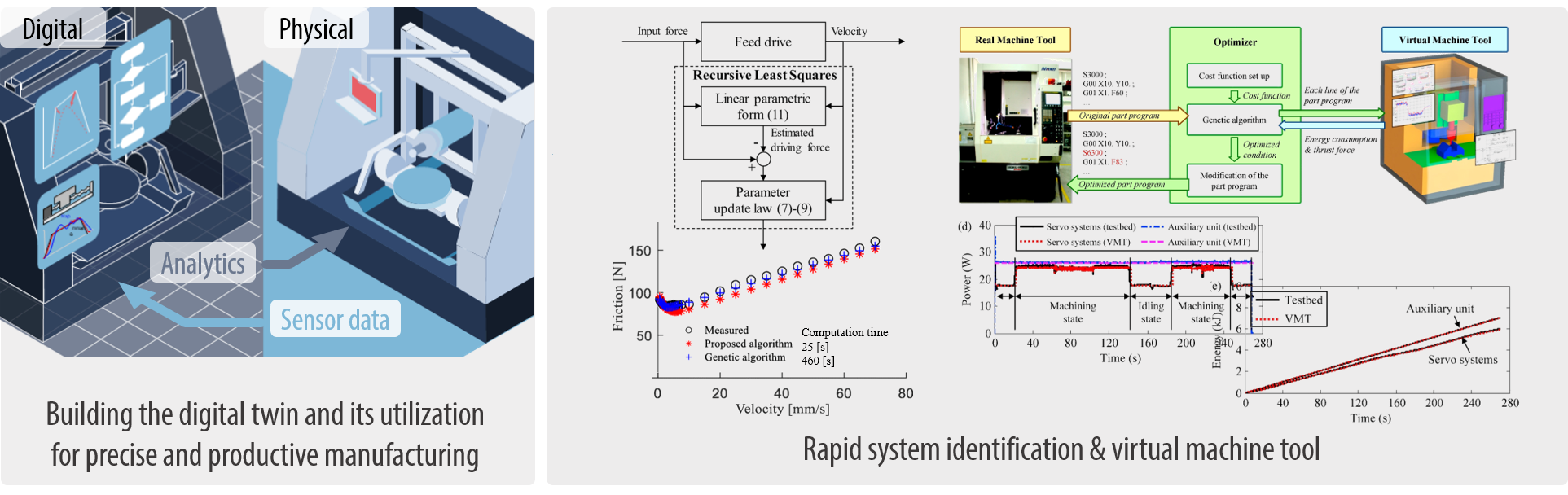
Robot Machining
4차 산업혁명의 시대가 도래함으로써 자동화 공장을 구현하기 위한 다양한 연구들이 진행되고 있다. 이 중 필수 요소 기술의 하나로 꼽히는 것이 산업용 로봇이며, 이와 함께 로봇 가공에 대한 연구가 세계적인 주목을 받고 있다. 로봇은 기존의 공작기계에 비해 넓고 효율적인 공간 활용이 가능하며, 높은 자유도를 지녀 다양한 위치에서의 가공이 가능하여, 형상의 제약 없이 어떠한 복잡한 형상의 제품도 가공해 낼 수 있는 미래형 생산 시스템의 열쇠가 된다. 그러나 현재 수준보다 더욱 높은 위치정밀도와 강성이 요구되어 이에 대한 연구를 진행중이다.
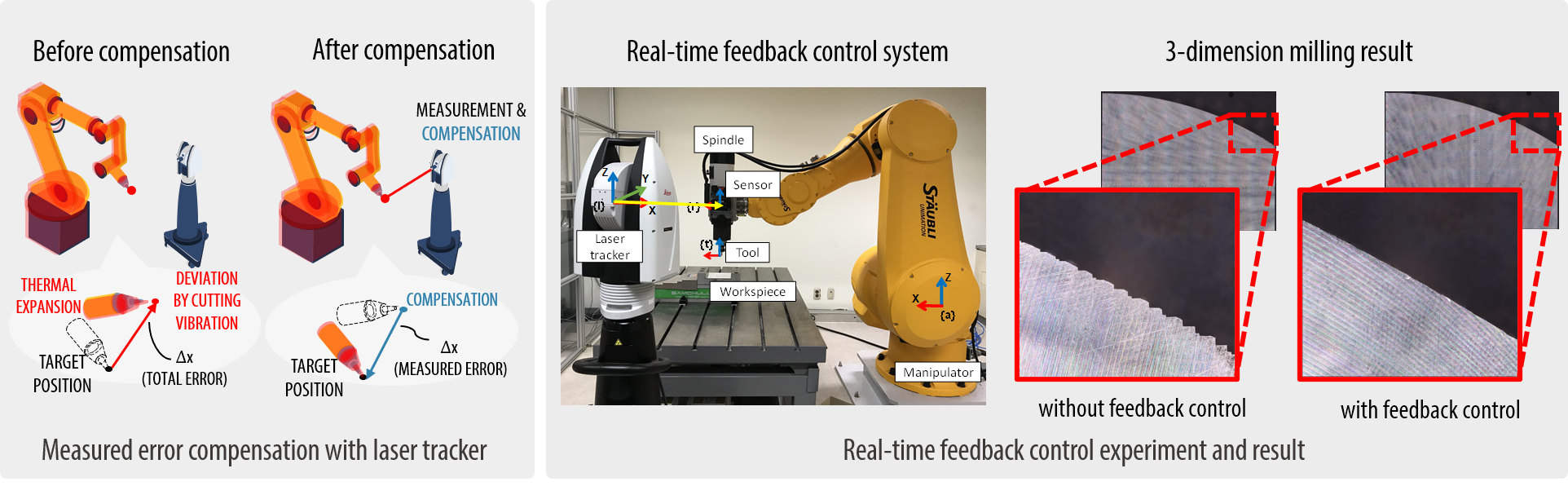
- Machining error compensation with stiffness model
- Kinematic parameter identification
- Precise control for robot machining
Machining error compensation with stiffness model
로봇은 기존 공작기계에 비해 강성이 매우 낮아 가공 중 큰 가공오차가 발생한다. 강성에 의한 가공 오차는 로봇의 링크나 각 축의 감속기 등이 휘면서 발생하는 것으로 측정이 매우 어렵다. 따라서 로봇 강성 모델을 이용하여 가공력에 의한 가공오차를 예측하고 보정하는 연구를 진행하고 있다. 힘/토크의 측정이 가능한 6자유도 센서를 이용하여 가공 시의 가공력을 측정하고, 측정된 가공력과 강성 모델을 이용하여 가공 오차를 예측 및 보정함으로써 가공 정밀도의 향상을 목표로 한다.Kinematic parameter identification
산업용 로봇은 링크와 축으로 구성되며, 각 링크의 길이, 축 간의 거리 및 기울기 등의 기하학적 파라미터를 통해 로봇의 끝 단의 위치가 계산이 된다. 따라서 기하학적 파라미터의 오차는 로봇 끝단에서 큰 위치오차를 발생시켜 가공 정밀도의 저하를 초래한다. 이를 해결하기 위해 본 연구실에서는 정밀 위치 측정기인 레이저 트래커를 이용하여 로봇 위치를 정밀하게 측정할 수 있는 시스템을 구축하였다. 지령 위치와 측정된 실제 위치를 비교하고, 그 오차를 줄임으로써 정확한 기하학적 파라미터를 식별하는 연구를 수행하고 있다.
Precise control for robot machining
로봇 가공 시 기하학적 파라미터의 오차, 가공력에 의한 변형 오차, 열변위에 의한 오차 등 다양한 원인에 의해 큰 위치오차가 발생한다. 따라서 다양한 방법으로 위치 오차를 예측하고, 기존의 위치경로에 보상함으로써 가공 정밀도를 향상시킬 수 있다. 그러나 상용 로봇 제어기의 제어 알고리즘을 수정하는 것은 제조사에 의해 제한된다. 따라서 본 연구실에서는 위치 제어기에 보상 값을 입력할 수 있도록 별도의 시스템을 구축하였으며, 로봇의 위치를 측정할 수 있는 장비인 레이저 트래커와 연동하여 위치 오차를 계산 및 보상하는 연구를 수행하고 있다.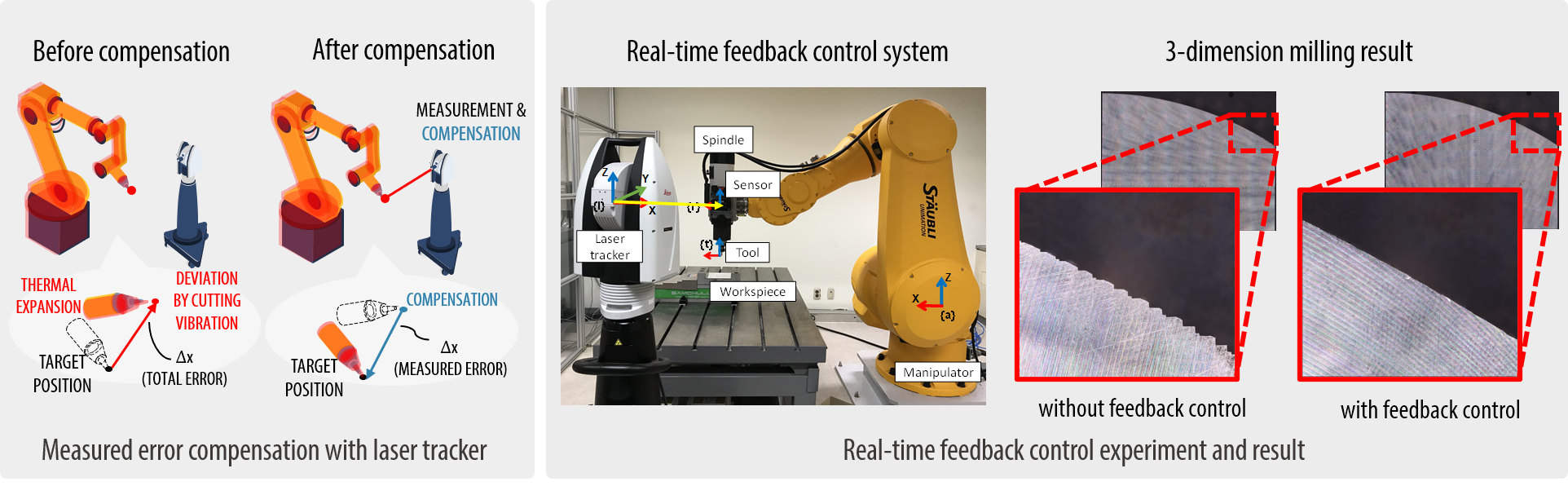
Human-Factory Interaction
공장과 인간이 유연하게 상호작용하기 위해서는 기계 장비를 다루는 작업자에게 직관성, 효율성, 정확성, 안전성을 갖춘 시스템이 필요하며, 이 시스템은 공장과 작업자 사이의 다리 역할을 한다. 본 연구실에서는 다음과 같은 다양한 시스템 개발 및 구축을 통해 효율적이고 직관적인 공장-사용자 상호 작용 환경 연구를 수행하고 있다.
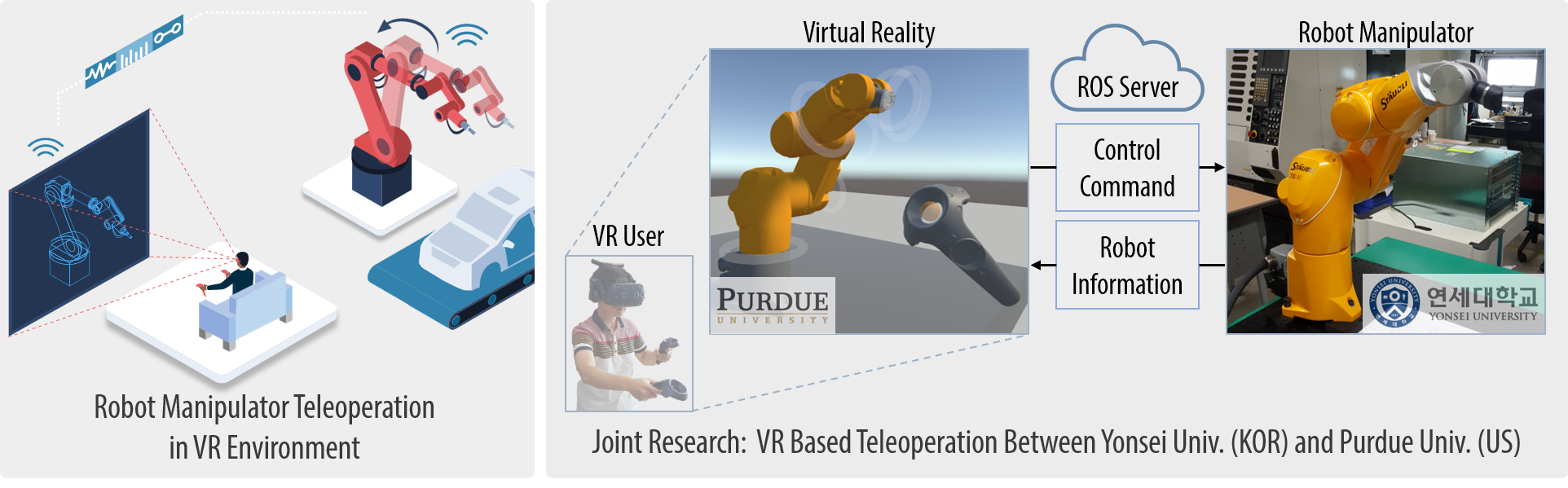
- Human – Machine Interface for Multipurpose
- Human – Machine Interface Using Computer Vision
- VR (Virtual Reality) Based Teleoperation
Human-Machine Interface for Multipurpose
HMI (Human-Machine Interface)란 인간과 기계의 상호작용의 약자로 사용자에게 기기, 프로그램, 시스템 등과의 통신을 가능하게 해주는 대시보드이다. 본 연구실에서는 GUI (Graphical User Interface) 기반 HMI를 개발하여, 기존에 고숙련 작업자들만 가능했던 기계 장비 작업을 용이하게 하며, 사용자 친화적인 인간-기계 상호 환경을 구축하고자 한다. 이를 위하여 자체 개발한 CNC (Computerized Numerical Control) 제어 프로그램, 가공 공정 모니터링 및 최적화 프로그램, 로봇 제어 프로그램이 적용된 HMI 연구 개발을 진행하고 있다.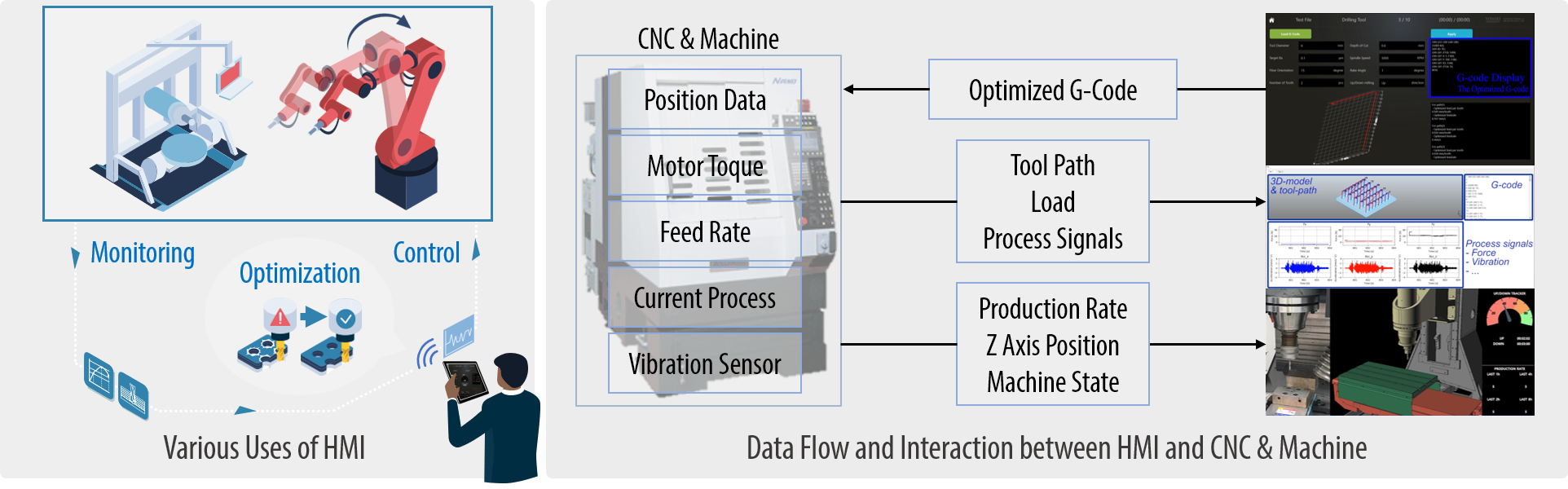
Human-Machine Interface Using Computer Vision
다양한 기계를 한 명의 작업자가 효율적으로 관리하고 다루기 위하여 Computer vision을 활용한 HMI 시스템을 연구하고 있다. 카메라를 통해 사용자 눈을 추적하여 시선을 계산하고 사용자의 시점에 맞추어 스마트 안경이나 투명 디스플레이에 정보를 투영함으로써 직관적인 정보를 전달하는 기술을 연구 중에 있다. 또한, 스마트 안경의 카메라를 통해 사용자의 손과 다른 사람의 손을 구분하여 다른 사람의 기계 조작으로 인한 사고를 방지하는 연구도 수행하고 있다.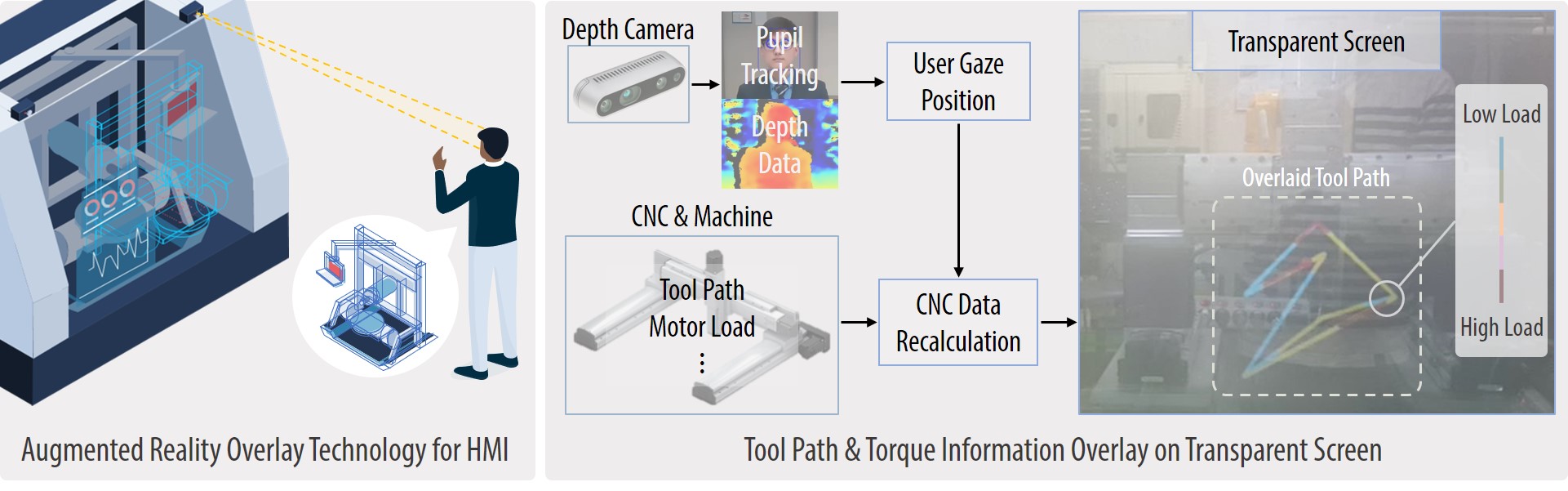
VR (Virtual Reality) Based Teleoperation
Teleoperation이란 기계나 시스템을 원거리에서 조작하는 것을 의미한다. 사람에 의한 teleoperation은 사람의 정교함, 숙련도, 배경에 대한 높은 지식을 로봇에 적용시킬 수 있다는 점에서 연구가 필요하며 여러 teleoperation 방법들 중, 본 연구실은 VR기기를 이용한 teleoperation을 통해 가상현실 내에 로봇 모델을 삽입하여 이를 통해 실제 로봇을 사용자가 조작하고 모니터링할 수 있는 시스템을 개발하였다. 이를 통하여 3D로 이루어진 세상을 2D interface로 연결하여 조작하는 기존 teleoperation의 한계를 사용자의 몰입감, 조작의 직관성 측면에서 개선하고자 한다. 나아가 해당 시스템을 이용하여 사용자에게 시점의 자유를 주며, 더 정밀하고 자연스러운 로봇의 움직임을 구현하는 연구를 미국 퍼듀대학교와 활발하게 교류하며 공동으로 수행하고 있다.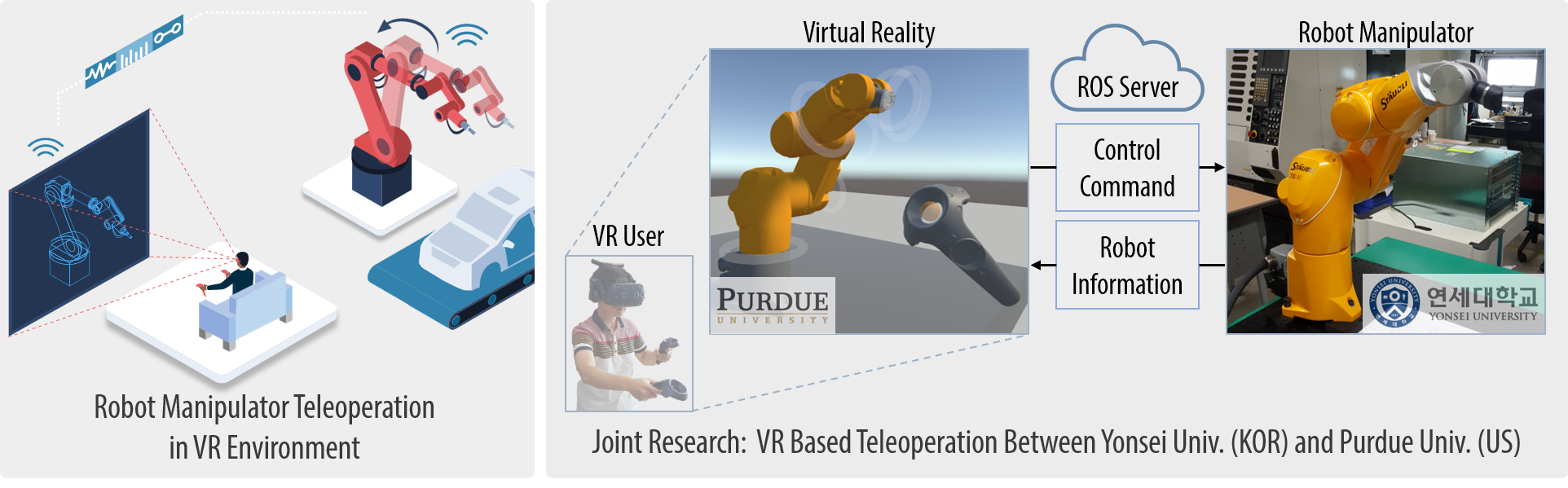
Manufacturing Processes
최근 산업에서 우수한 기계적, 화학적 성질로 사용이 증가하고 있는 탄소섬유복합재, 티타늄 합금 등과 같은 재료는 기계적 가공이 어려워 난삭재 (difficult-to-cut material)라 불린다. 본 연구실에선 이러한 난삭재들의 무결점 가공을 목표로 가공 시 발생하는 현상을 수학적으로 모델링하고 이를 바탕으로 가공 품질 및 산업에서의 생산성을 증가시키기 위한 연구를 수행하고 있다.
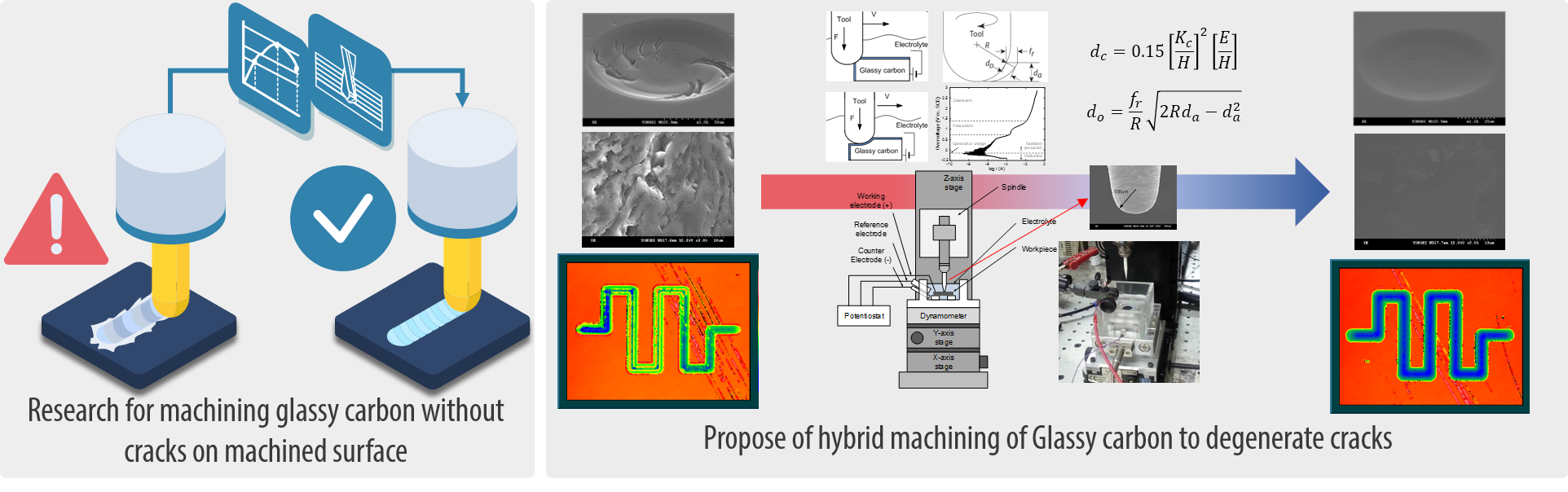
Composite material machining
CFRP (탄소섬유복합재, Carbon fiber reinforced plastic)는 일반 금속에 비해 무게 대비 강도가 높기에 차량, 항공기 등 차세대 산업용 구조재로 각광받는 재료이다. 하지만 고경도의 탄소섬유와 이방성의 성질로 인해 드릴링, 밀링과 같은 기계가공 시 박리 및 섬유 뜯김과 같은 결함이 쉽게 발생한다. 따라서 무결점 가공 구현을 목표로 절삭 시 재료의 기계적 거동에 기반한 고품질 가공 모델을 제시하는 연구를 수행하고 있다. 이를 바탕으로 실제 산업에서 고품질 복합재 가공을 위한 어플리케이션 S/W 개발을 수행하고 있다. 또한 미국의 퍼듀대학교와 공동으로 복합재 가공관련 연구를 활발히 수행하고 있으며 이를 위해 최근 관련 연구자를 직접 파견한 바 있다.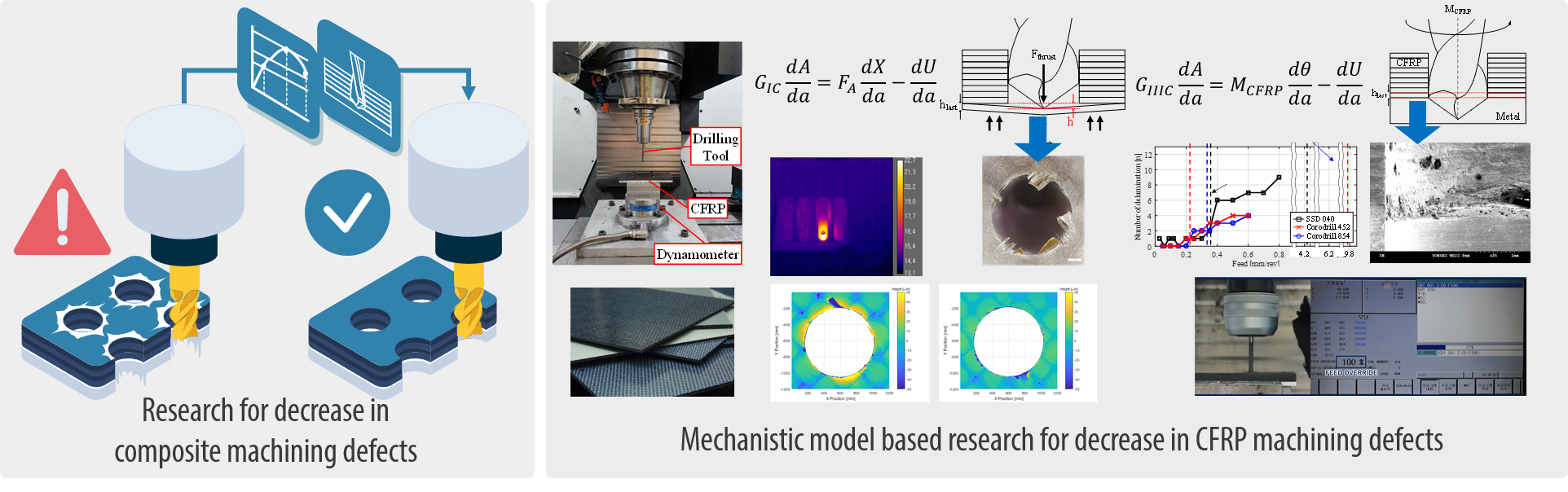
Ti alloy machining
티타늄합금은 우수한 기계적 특징으로 인해 항공기, 우주선, 의학 장비 등 다양한 분야에서의 사용이 증가하고 있는 소재이다. 하지만 가공 중 고온이 발생하여 가공 칩이 공구에 점착되고 재료의 상변이도 발생하여 공구마모 증가 및 가공 품질 저하를 야기한다. 이러한 문제를 해결하기 위해 액화질소를 이용한 극저온 간접 냉각 가공 방식을 제안 및 가공 특성에 대한 연구를 수행하고 있다.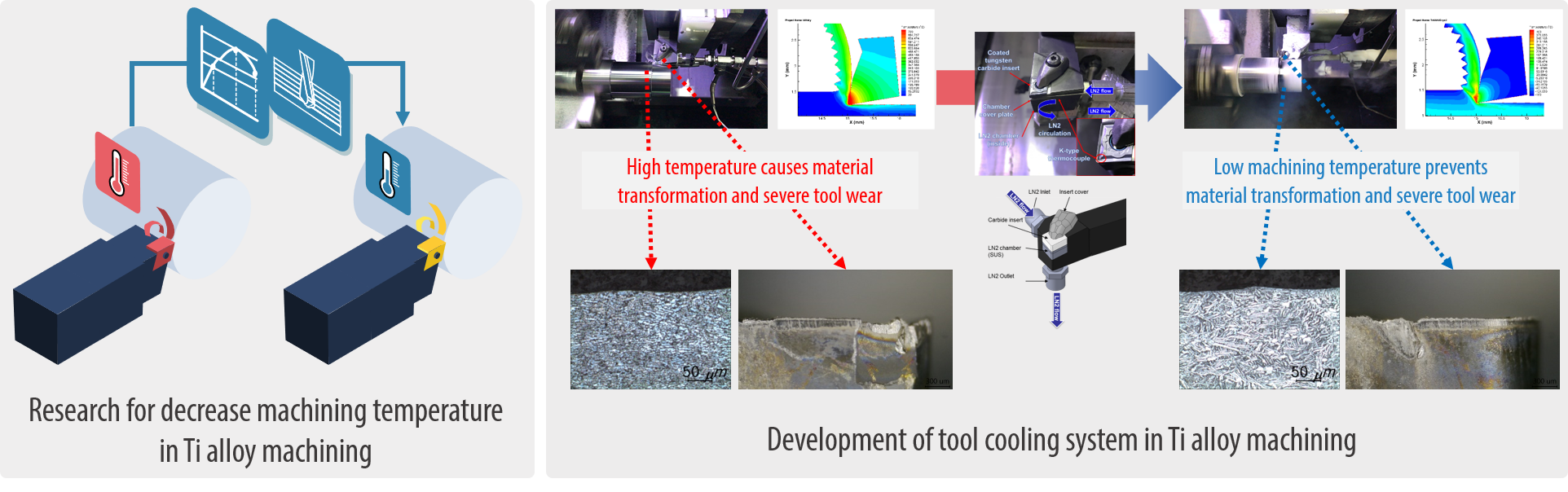
Glassy carbon machining
GC는 높은 경도와 화학적 안정성을 가진 전도성 소재로 배터리 및 렌즈 몰드 분야에서의 많은 수요가 기대되는 재료이다. 하지만 가공시의 깨짐 현상에 의해 우수한 표면 품질의 가공물을 얻기 위해서는 이온빔 가공과 같은 고비용 및 저속의 방법으로 주로 가공하고 있다. 이러한 문제를 해결하기 위해 전기화학적 산화 가공법을 이용하여 우수한 표면 품질을 유지하며 빠른 가공이 가능한 연구를 하였으며 보다 높은 가공 효율을 위해 Elliptical vibration cutting method (EVC)를 응용한 연구를 수행하고 있다.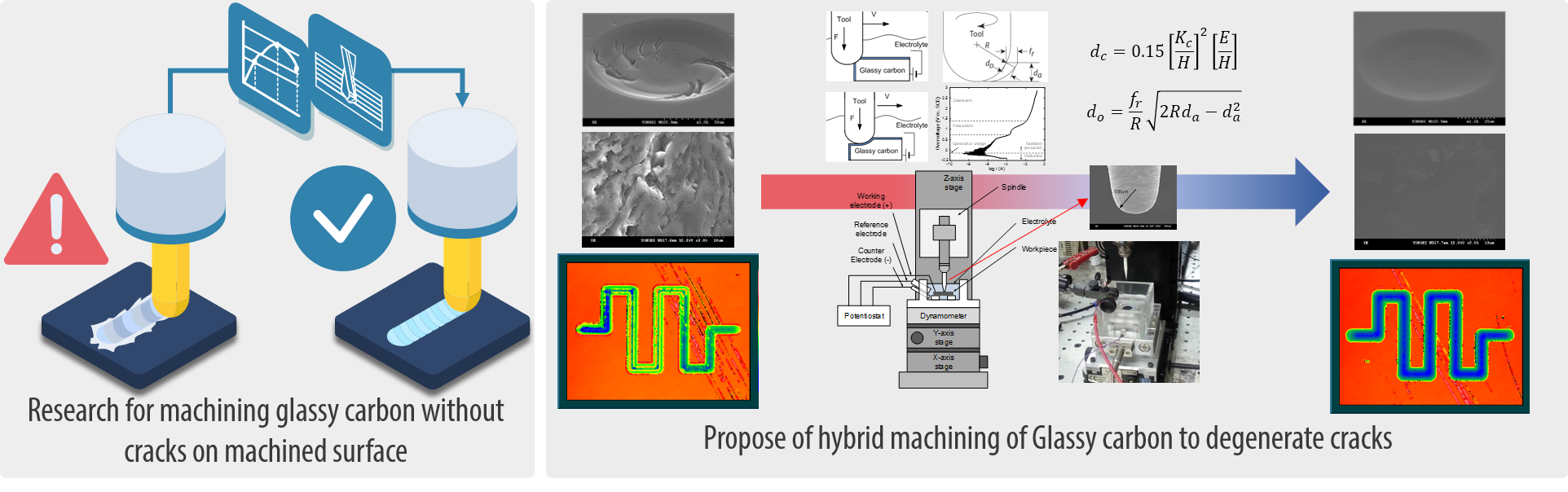
PAST RESEARCH
System control
Micro factory
Haptic
Virtual micro manufacturing
Energy autonomos system
Electrical discharge machining (EDM)
Magnetorheological finishing (MR finishing)
Nano patterning
Multi beam system
System control
가공 공정의 안정성 향상, 효율성 및 생산성 향상, 가공형상 정밀도를 저하시키는 공정 문제점 보완 등을 위해 가공공정의 제어가 필요하다. 본 연구실에서는 다음과 같은 다양한 가공공정의 제어와 이를 위한 시스템을 설계·구축하는 연구를 수행하고 있다.
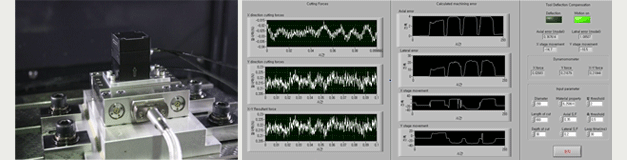
- EDM 밀링 가공에서의 실시간 펄스 모니터링을 통한 공구마모 보정
- 마이크로 밀링 공정에서의 ploughing 발생의 실시간 감지
- 밀링 가공에서의 공구휨 실시간 예측과 보정
EDM 밀링 가공에서의 실시간 펄스 모니터링을 통한 공구마모 보
EDM 밀링 공정에서의 공구마모 보정 기술의 일환으로 실시간 펄스 모니터링 시스템을 연구하고 있다. 방전펄스수와 재료제거량의 관계, 펄스빈도수와 방전간극간의 관계를 모델링하였고, 실시간 모니터링을 위하여 빠른 펄스카운팅 알고리즘을 고안하여 펄스빈도수를 측정함으로써 방전간극을 제어하고 공구마모를 보정하는 가공시스템을 구축하였다. 이 방법을 통해 블라인드홀의 가공깊이, 밀링공정에서의 공구마모 보정, 장비나 가공물 셋업오차에 의한 기울어진 가공물의 형상정밀도 저하를 보정하였다.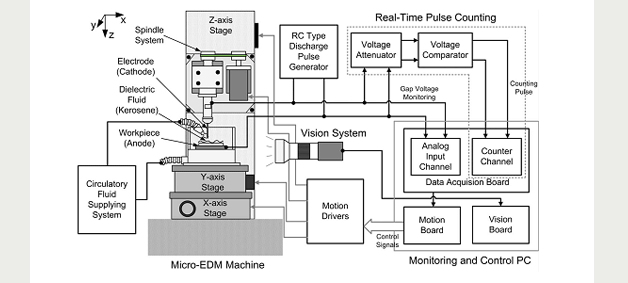
마이크로 밀링 공정에서의 ploughing 발생의 실시간 감지
플로잉(ploughing) 현상은 밀링 가공에서 무딘 공구 끝단에 의해 재료가 가공되지 않고 탄성 또는 소성 변형되는 것을 의미한다. 마이크로 밀링 공정에서는 작은 공구강성으로 인해 작은 절삭 피드를 적용하여야 하기 때문에 플로잉이 발생할 수 있다. 따라서, 마이크로 밀링 공정에서 플로잉의 발생을 감지하기 위한 방법을 연구하고 있다. 플로잉이 발생할 때의 절삭력 변화를 신호처리 기법을 이용해 분석하여 플로잉의 발생 여부를 실시간으로 모니터링한다. 나아가 실시간으로 플로잉 현상을 회피할 수 있는 가공 시스템을 연구 중에 있다.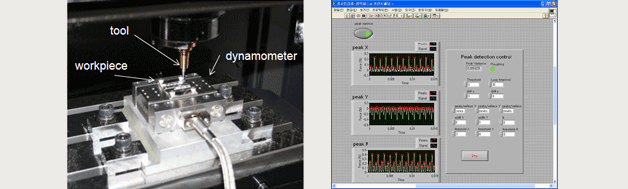
밀링 가공에서의 공구휨 실시간 예측과 보정
마이크로 밀링 공구의 강성이 작기 때문에 공구는 가공 중 쉽게 휘게 된다. 이러한 공구 휨 문제는 가공물의 형상 정밀도를 저하시키고, 빠른 가공 속도를 저해하여 가공효율을 떨어드리게 된다. 이를 해결하기 위해, 절삭력에 따른 공구휨의 발생을 모델링하였고, 모델과 정밀 스테이지를 이용하여 공구휨을 실시간으로 보정할 수 있는 시스템을 연구하고 있다.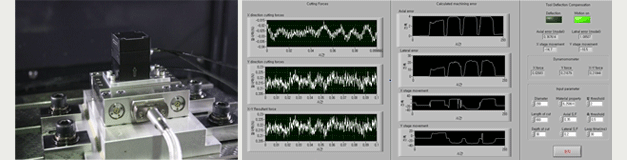
Micro factory
기계 가공 부품의 다품종화, 소형화에 대응하기 위한 새로운 가공 시스템을 구축하기 위해 자원절약, 공간 절약형 공작기계인 마이크로팩토리에 대한 연구를 수행하고 있다. 마이크로팩토리는 공정을 모듈화하여 시스템을 구축하므로 제품생산에 유연성을 가진다. 미세 방전 가공을 마이크로팩토리에 적용하기 위해 방전 가공의 각 유닛 소형화, 각종 유닛들의 움직임을 모니터링하기 위한 비젼 모니터링, 마이크로 팩토리의 재구성성(reconfigurability)을 고려한 시스템 제어기에 대한 연구를 수행하고 있다.
마이크로 택토리는 제품생산에 유연성을 가져야 하므로, 모듈 간의 재구성이 용이해야 하며, 사용자가 사용하기 편해야 한다. 그러므로, 마이크로 팩토리 제어기는 재구성을 하는데 있어서 하드웨어를 직접 조정하는 것을 최대한 배제한 소프트웨어 기반이 되어야 한다. 이를 위해 멀티에이전트(multi-agent) 시스템과 계층구조(layer structure)에 기반한 마이크로 팩토리 제어기를 개발하고 있다.

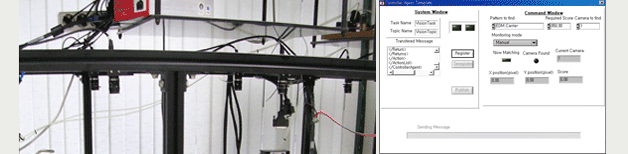
Haptic
Haptic Interface는 물리적 장치를 이용하여 직접적인 접촉 없이 사람에게 촉각 정보를 전달하는 시스템을 의미한다. 본 연구실에서는 Haptic Interface를 이용하여 스테이지를 제어하고, 가공물을 손을 통해 직접 측정하고, 측정된 형상을 촉감으로 느낄 수 있는 시스템을 연구하고 있다.
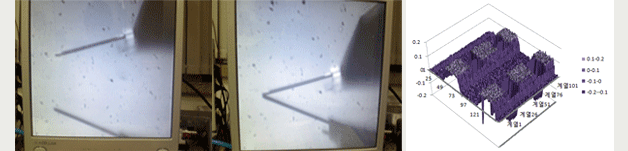
- Haptic device를 이용한 스테이지 제어
- Haptic force feedback을 이용한 표면형상 확인
- Haptic device를 이용한 3차원 형상의 측정
Haptic device를 이용한 스테이지 제어
Haptic 내부의 6개 엔코더를 이용하여 2축 스테이지를 제어하는 시스템을 연구하고 있다. 사용자가 haptic 의 pen을 이동시킴으로써 실제 스테이지를 움직이고, 제어 프로그램에 이동 범위와 최대이동 속도를 설정하여 이를 넘어갈 경우 haptic 내부의 모터를 이용한 force feedback 기능을 이용하여 사용자에게 신호를 주고 스테이지의 이동을 제어한다.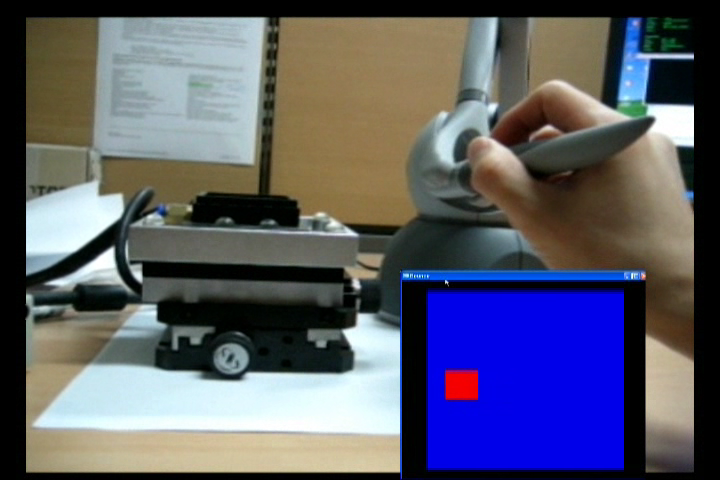
Haptic force feedback을 이용한 표면형상 확인
3차원 표면형상 측정장비로 측정된 표면형상을 시각적으로 확인하는 것을 넘어, haptic의 force feedback 기능을 이용하여 촉감으로 측정물의 3차원 형상을 확인할 수 있는 시스템을 연구하고 있다.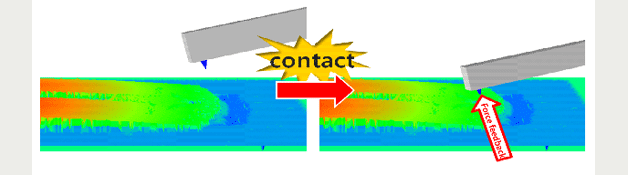
Haptic device를 이용한 3차원 형상의 측정
Haptic을 이용하여 AFM 탐침의 위치를 제어하여 3차원 형상을 측정하는 연구를 수행하고 있다. ?기존의 AFM 측정 방식에 haptic을 적용하여 사용자가 보다 편하게 AFM tip의 위치를 제어할 수 있고, 표면의 형상을 손으로 직접 느낄 수 있다.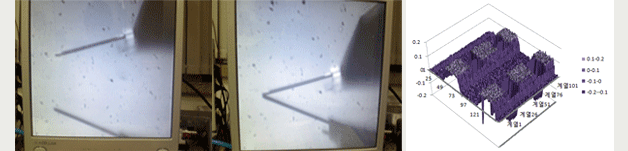
Virtual micro manufacturing
Virtual machining이란 가공현상을 실제와 유사하게 시뮬레이션하는 것을 말하며, 이를 통해 가공 중의 여러 가지 정보를 산출할 수 있으며, 공정 최적화 등의 목적으로 이용할 수 있다. 본 연구실에서는 마이크로 EDM 공정의 virtual machining을 연구하고 있다.

Virtual EDM simulator 개발과 이를 통한 마이크로 밀링 방전가공에서의 공구마모 보정
EDM 가공에서 재료제거의 단위인 단발방전에 의한 크레이터의 생성 원리 및 형상 등의 정보를 얻기 위해 FEM을 통한 열전달 해석을 수행하고, 그 결과와 공구와 가공물간의 기하학적 관계를 토대로 EDM 밀링 가공에서의 공구마모와 가공물의 가공형상을 예측하는 시뮬레이션 프로그램을 개발하였다. 또한, 이를 확장하여 EDM 밀링 공정에서 공구마모를 보정하여 원하는 형상을 가공할 수 있는 공구경로를 생성하는 CAM소프트웨어를 연구 중에 있다.
Energy autonomos system
자가발전 모니터링 시스템은 외부환경을 통하여 에너지를 생성하고 생성된 에너지를 이용하여 외부환경의 변화를 실시간으로 감시하는 시스템이다. 시스템은 에너지 생성을 위한 자가발전 센서부, 외부환경의 변화를 모니터링하기 위한 센서 데이터 처리부 그리고 데이터 전송을 위한 무선 통신부로 구성된다.
본 연구실에서는 파이프 속 유체 흐름을 감시하기 위한 인파이프 자가발전 모니터링 시스템을 연구하고 있다. 에너지 생성과 외부환경의 변화를 감지하는 센서를 개발하고 있으며, 이를 위해 데이터 처리 및 무선통신을 위한 에너지를 고려하여 센서의 구조 설계를 수행하고 있다. 인식된 데이터를 처리하는 기술과 처리된 데이터를 무선으로 사용자에게 전송해 주는 기술에 대한 연구도 수행하고 있다. 자가발전 모니터링 시스템은 파이프라인의 상태 감시 뿐만 아니라, 가공 중 공작기계 상태 감시, 건물이나 구조물의 균열 상태 감시에 활용될 수 있다.
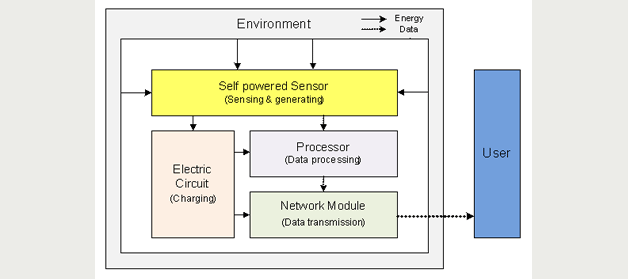
Electrical discharge machining (EDM)
방전 가공 (EDM; Eltrical Discharge Machining)은 플라즈마의 높은 에너지를 이용하여 전도체인 재료를 가공하는 정밀 가공 기술로써, 비접촉 가공이라는 장점으로 인해 널리 활용되고 있다.
본 연구실에서는 EDM가공에서 공구마모 등의 공정 문제 해결, 가공 정밀도 향상, 공정 최적화를 위해 가공 원리 규명, 가공 인자 분석, 미세 방전가공 시스템 제작 및 제어 등의 다양한 연구를 진행 중에 있다.
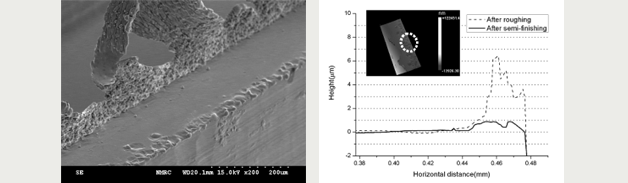
- EDM 가공 메커니즘에 관한 연구
- 공구 마모의 예측과 보정
- PMEDM (Powder mixed EDM)
- 방전 회로 설계
- 미세 방전 디버링 공정
EDM 가공 메커니즘에 관한 연구
EDM에서 가공물 제거는 전기적 에너지(전압, 전류, 빈도수, 온타임), 절연액·재료 물성 등의 복잡한 인자에 의해 영향을 받는다. 이를 규명하기 위해 FEM 열해석을 이용한 재료제거, 플라즈마 채널의 전기역학적 모델 등을 연구하고 있다.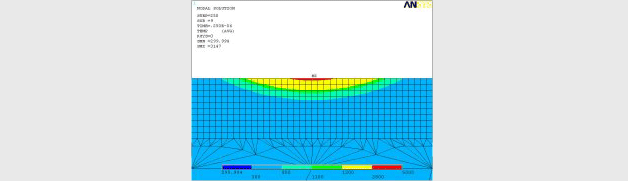
공구 마모의 예측과 보정
EDM은 열에너지를 기반으로 한 가공 기술이기 때문에, 가공물 뿐만 아니라 공구로 사용되는 전극 또한 열에 의해 제거되게 된다. 이러한 공구마모의 문제를 해결하기 위해 시뮬레이션 기반의 공구마모 예측·보정 기법과 방전 frequency 제어를 통한 실시간 공구마모 보정 기법을 연구하고 있다.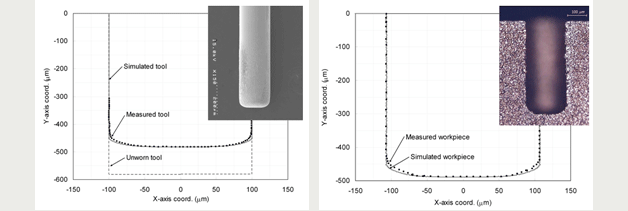
PMEDM (Powder mixed EDM)
절연액에 미세 파우더를 첨가하여 가공품질을 향상시키는 연구를 진행하고 있다. 이를 위해, 파우더를 첨가하였을 때 절연액의 열전달 특성의 변화와 그에 따른 가공에너지와 가공 표면거칠기 등의 관계를 분석한다.방전 회로 설계
EDM 공정에서 보다 안정적이고 균일한 에너지를 제공하기 위해 기존의 RC타입 방전회로를 개선하는 연구를 수행하고 있다.미세 방전 디버링 공정
미세부품의 밀링 가공 중에 발생한 버(burr)는 가공물의 손상 때문에 기계적인 방법으로 제거하기가 어렵다. EDM은 비접촉식 가공이기 때문에 가공력을 거의 무시할 수 있으므로 이러한 특성을 이용해 버를 효과적으로 제거하기 위한 공정과 시스템을 연구하고 있다.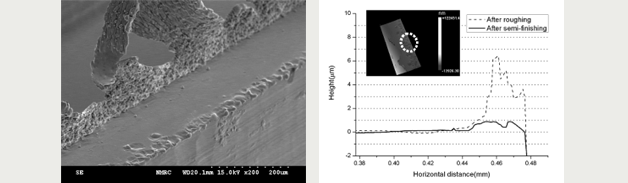
Magnetorheological finishing (MR finishing)
자기유변유체 (Magnetorheological (MR) Fluid)는 자화가능한 미세입자와 물 또는 기름 등의 유체가 혼합된 것을 뜻하며, 외부 자기장에 의해 점도가 조절되는 특징을 가지고 있다. 이러한 특성으로 자기유변유체는 댐퍼, 브레이크, 연마 등 다양한 분야에 폭넓게 사용되고 있다. 본 연구실에서는 자기유변유체의 거동특성을 분석하고 이를 이용한 자기유변연마공정을 연구하고 있다.
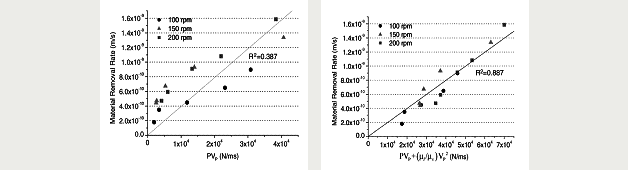
자기유변유체의 정자기 거동모델 및 자기유변연마공정의 재료제거모델
자기유변연마공정은 자기유변유체의 거동특성에 의해 영향을 받는다. 자기유변유체의 거동특성을 분석하기 위해 자기장하에서의 자기유변유체의 물리적 특성을 수학적으로 모델링하고, 이를 바탕으로 자기유변연마공정에서의 재료제거율 예측 모델에 대해 연구하고 있다.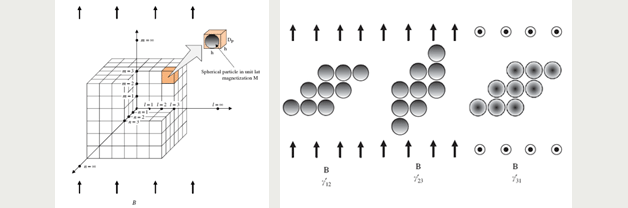
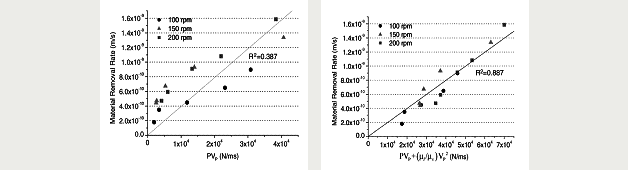
Nano patterning
본 연구실에서는 집속이온빔(Focused ion beam, FIB) 가공 및 복합 공정에 대한 가공정밀도 향상과 공정 개선을 위한 연구와 이를 이용한 나노 단위의 형상 및 패턴을 가지는 구조물 제작에 대한 다양한 연구를 진행하고 있다.
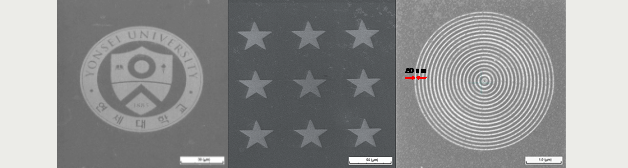
- 집속이온빔 공정의 시뮬레이션을 통한 가공형상 예측
- 증착을 이용한 미세 구조물 제작
- 이미지 프로세싱을 이용한 가공형상의 보정
- 국소적 이온 주입을 이용한 복합 공정에 의한 구조물 제작
집속이온빔 공정의 시뮬레이션을 통한 가공형상 예측
집속이온빔 가공에서 형상정밀도 향상을 위해 빔조사 path, 빔의 가우시안 분포, 입사각, 재증착 현상 등을 고려하여 공정을 모델링하고 이를 통해 가공형상를 기하학적으로 예측하는 시뮬레이션 기법을 개발하였다. 개발된 시뮬레이션 기법을 바탕으로 형상정밀도를 향상시킬 수 있는 가공 보정 방법을 연구 중에 있다.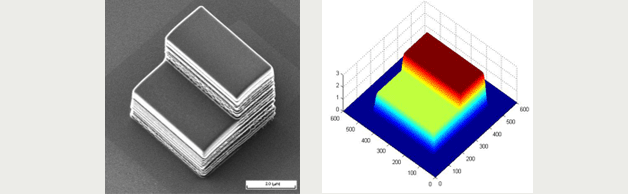
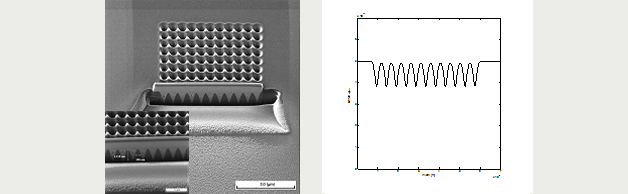
증착을 이용한 미세 구조물 제작
빔 조사 path와 세기 등을 제어하여 수십 나노 정밀도로 재료를 증착하여 원하는 형상을 형성할 수 있다. 이를 이용하여 다양한 기능을 가지는 나노 구조물에 대한 연구를 수행하고 있다.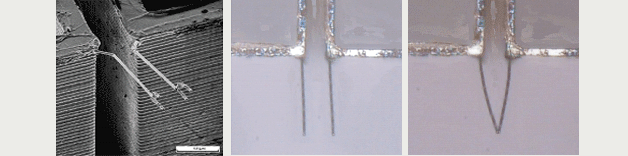
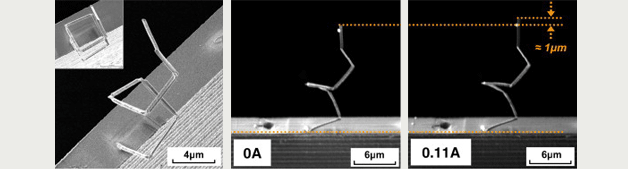
이미지 프로세싱을 이용한 가공형상의 보정
이온빔을 이용한 에칭 시 스퍼터링된 재료의 일부가 다시 가공면에 붙는 재증착 현상이 형상 정밀도를 저해하는 요소로 작용한다. 이미지 프로세싱을 이용하여 가공 형상 데이터를 입력 받은 후 가공 오차를 다시 보정하여 실제 원하는 형상을 가공하는 제어 기술을 연구하고 있다.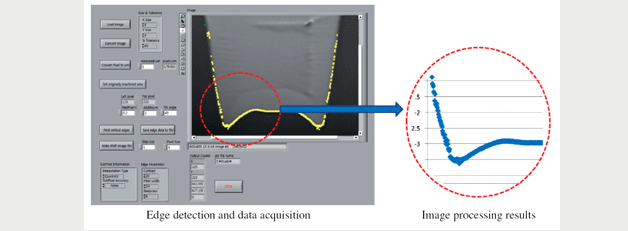
국소적 이온 주입을 이용한 복합 공정에 의한 구조물 제작
집속이온빔을 이용해 국소적으로 재료에 이온을 주입하여 모재의 물성을 변화시켜 미세 구조물을 제작하는 복합공정을 연구하고 있다.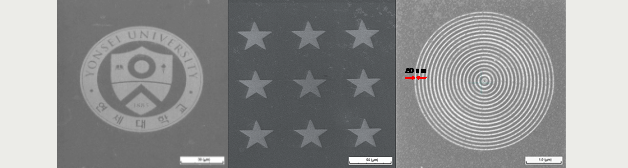
Multi beam system
본 연구실에서는 기존의 집속이온빔 가공의 낮은 생산성을 극복하기 위해 다중빔 (multi beam) 방식의 가공 시스템을 개발하고 있으며, 이를 위해 다음과 같은 연구를 진행하고 있다.
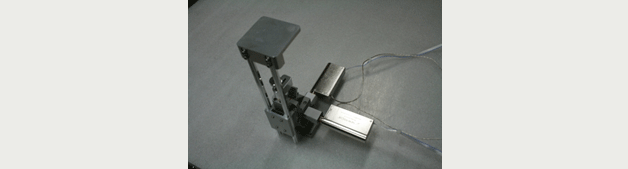
- 대면적 이온소스
- 가변 aperture 설계
- 이온빔 광학계 설계 및 해석
- 스테이지 제어
대면적 이온소스
기존의 집속이온빔 장비에서 이온빔을 방출시키기 위해 사용되는 이온소스는 액체갈륨을 이용하는 liquid metal ion source (LMIS)로 텅스텐으로 만들어진 팁에 액체갈륨을 저장하고, 강한 전기장을 걸어 갈륨이온을 발생하는 이온소스이다. LMIS의 경우 빔의 발생 영역이 좁아 빔 조사면적이 큰 다중이온빔 장비에 적합하지 않다. 따라서 빔 발생영역을 증가시키기 위해 아르곤 이온을 발생시키는 penning type 과 RF type의 기체이온소스를 연구하고 있다.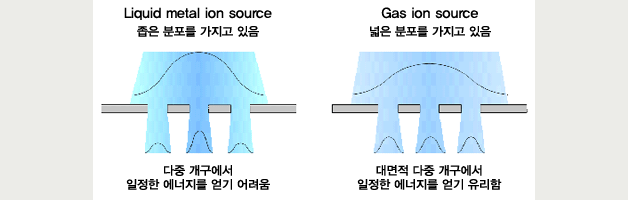
가변 aperture 설계
이온소스에서 방출된 이온빔은 다수의 개구를 가진 어퍼쳐를 통해 다수의 빔으로 분할된다. 이때 어퍼쳐는 이온빔에 의한 손상을 받게 되며, 이온빔에 의한 손상 정도는 재료에 따라 다르게 나타난다. 재료에 따른 손상 정도를 분석하여 이온빔 어퍼쳐에 적합한 재료를 연구하고 있다. 또한, 다중 개구에 전극을 설치해 빔을 제어할 수 있는 가변 aperture를 연구하고 있다. 이를 위해, 전기장 해석을 통해 전극 형상을 설계하고 있다.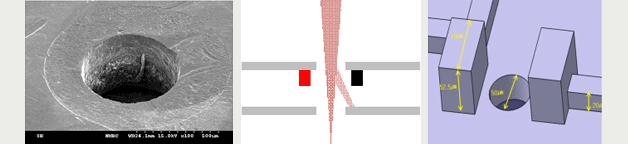
이온빔 광학계 설계 및 해석
다중 개구에 의해 분할된 이온빔은 정전렌즈로 구성된 이온빔 광학계를 통해 집속되어 시편에 조사된다. 따라서 다중이온빔의 집속을 위한 새로운 구조의 광학계를 설계하고 있다. 이를 위해 이온빔의 거동을 시뮬레이션하여 이온의 종류, 이온의 에너지, 광학계의 구조, 전기장의 세기 등을 해석하고 있다.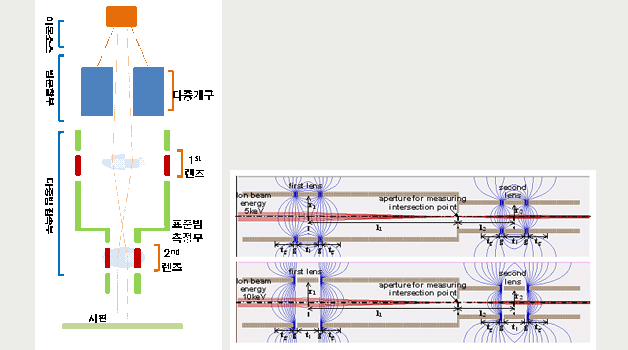
스테이지 제어
원하는 패턴을 가공하기 위해 스테이지를 제작하고, 패턴의 형상, 빔의 크기와 조사시간, 재료에 따른 가공량 등을 고려하여 스테이지 이송속도와 경로를 제어하는 연구를 진행하고 있다.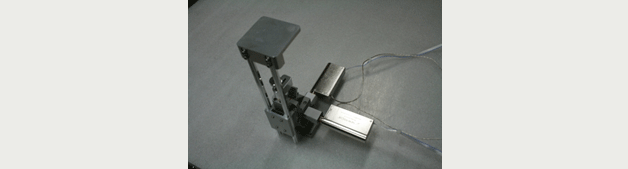